可靠的视觉表面检查助您获得高质量的制造结果
视觉表面检查可检测到根据工艺要求认定的缺陷,帮助您生产出高品质的工件。
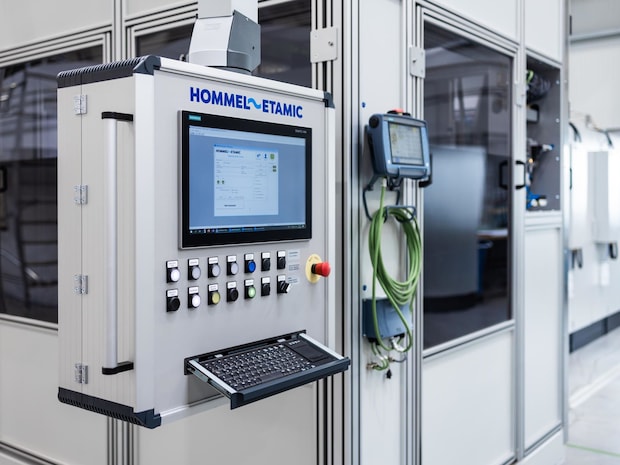
Visionline multi-sensor machine
Our Visionline solutions provide you with a wide range of application options for optical surface inspection.
Optical surface inspection from HOMMEL ETAMIC delivers 100 % quality control in the production of workpieces, ensuring consistently high quality. The procedure is not dependent on the operator and is reliable. The high-resolution camera systems precisely check your workpieces and detect the smallest flaws. Thanks to the high inspection rate, the inspection can be integrated into the line, and matches cycle times, saving you costs in production.
To ensure that the system best meets your requirements, we offer various versions with individually assembled sensors for bore inspection and plane surface inspection - adapted to your needs. The machine can either be loaded manually offline or is available as an automated inline version. The robot-assisted version ensures maximum flexibility. Thanks to our multi-sensor systems, you can effortlessly solve even complex inspection tasks without any problems.
Application example multi-sensor system
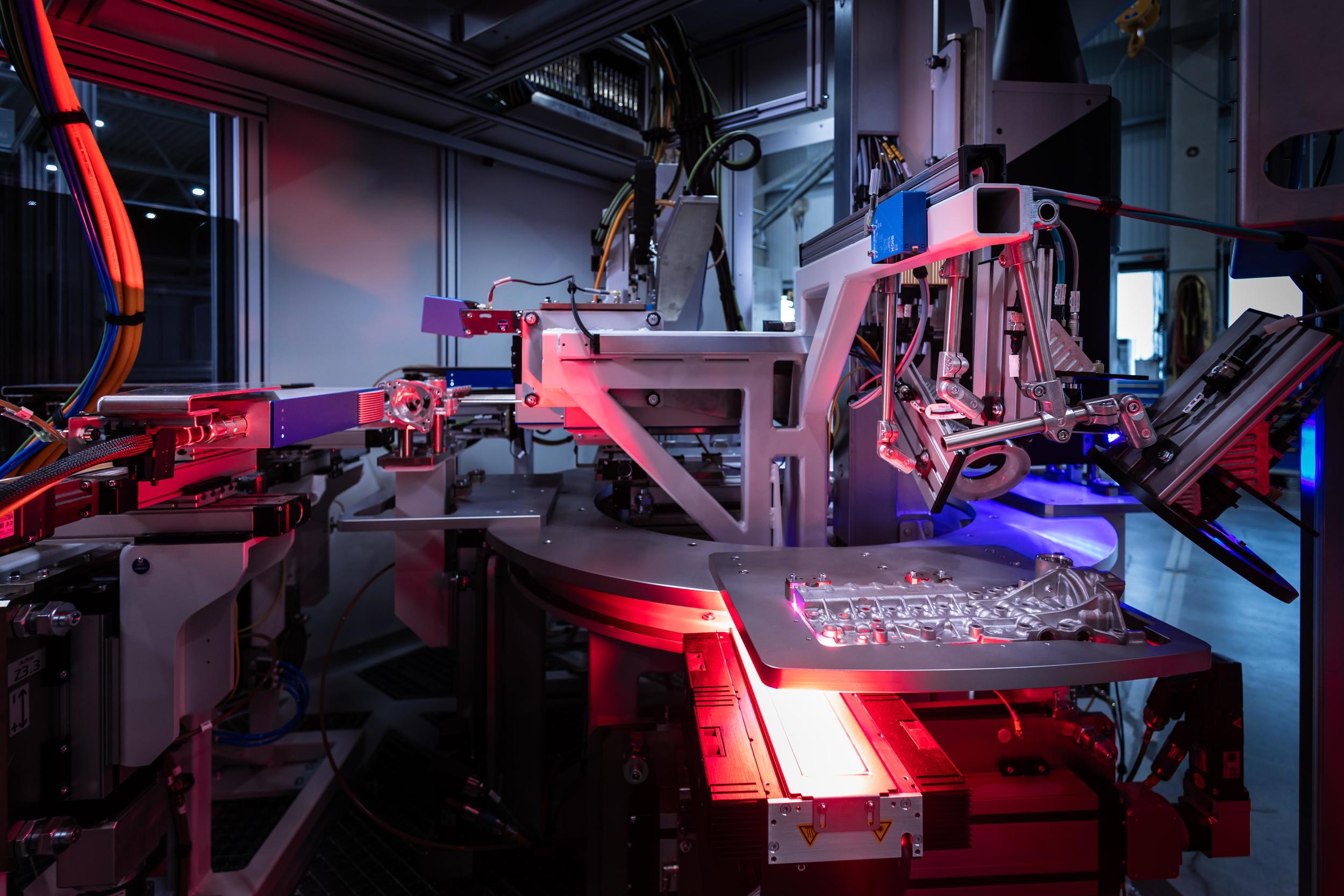
With Visionline solutions, inspection runs automatically and delivers operator-independent and reproducible results. This avoids the errors of visual inspection and ensures that only truly high-quality products are further processed and delivered.
Immediate inspection of all workpieces directly after the machining step allows statements to be made about the manufacturing quality. Feedback of the inspection results into the production process helps to identify and eliminate problems at an early stage.
Detection of smallest flaws
- Cavities
- Pores
- Scratches
- Recesses
- Spalling
- Burrs
Automated quality control with surface inspection systems
Standalone systems for optical bore inspection
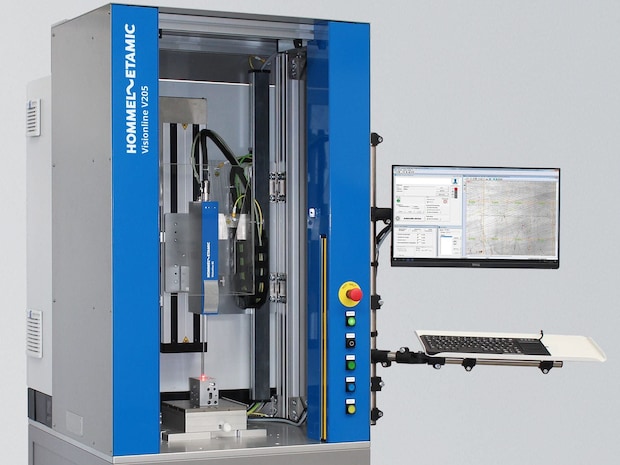
Visionline V200 | Standalone system for optical surface inspection
The systems for optical bore inspection in the Visionline V200 series deliver reliable and reproducible inspection results without operator influence. Thanks to their compact design and robust construction, they are suitable for offline inspection of bore surfaces in the production area. Equipped with a B5 or B20 sensor, the systems provide high-resolution, distortion-free images of bore surfaces and detect typical surface defects such as blowholes, pores, scratches or cavities. Optional X and Y axes ensure precise workpiece positioning and automated inspection runs.
Advantages
- Wear-free and dependable thanks to optical testing technology
- Fast inspection with short cycles
- Easy retooling of the system when changing workpieces
- Safety in case of misalignment of the workpiece thanks to collision protection
- Reduction of pseudo errors and unrecognized defects (slippage)
System features
- Compact with mimimum space requirement
- Light barrier for safe operation
- Testing of bore diameters of different sizes
- Proven technology with 360° optics
- Image pickup whilst in motion for fast results
- Head-on collision protection
- Connection to QDA systems possible
Downloads
Optical bore inspection
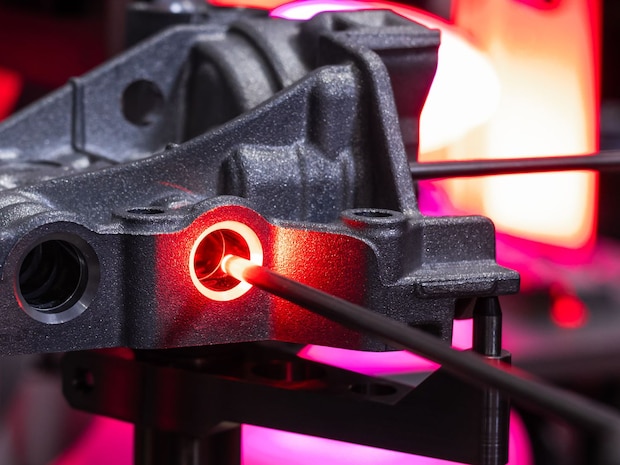
Visionline B5
Visionline B sensors are especially suitable for bore surfaces. They impress with their 360° all-round vision optics. In this automatic process, a CMOS sensor completely scans the inner surface of the bore and delivers high-resolution and high-contrast images. This allows for the detection of surface defects such as blowholes, porosity and scratches even during production. With Evovis Vision software, your employees evaluate the images easily and intuitively.
Innovative camera and illumination technology, adaptive dynamic masking, and high resolution enable automated 100 % inspection of bores within the required cycle time of the production process. The systems allow a fast inspection of the complete bore surfaces, as well as the classification of defect areas.
Sensors
- Visionline B5 for bores from 5 mm
- Visionline B20 for bores from 14 mm
- Visionline B100 for bores from 68 mm
Downloads
Optical inspection of plane surfaces
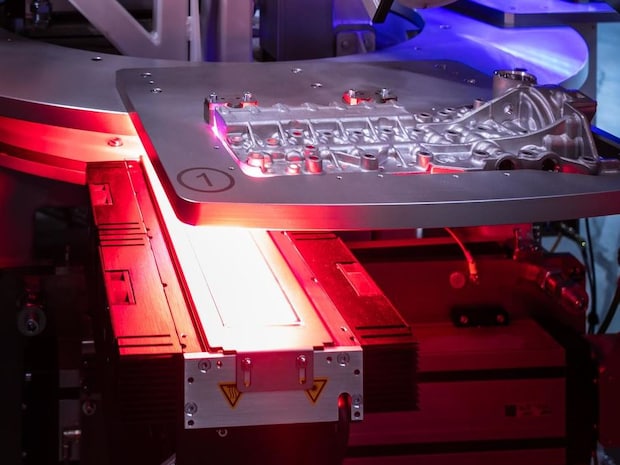
Inspecting plane surfaces
The Visionline F sensors are specially designed for the automatic inspection of plane surfaces. Thanks to the fly-over technology, image acquisition takes place in the movement at the correct cycle time, thus ensuring the shortest possible inspection times. Thanks to their high speed, they are therefore used for 100 % inspection of technical surfaces.
The plane surface sensor is moved over the workpiece and generates a high-contrast image of the machined surface. The innovative image recording technology determines a topography of the surface, making it possible to distinguish genuine surface defects and contamination with a high level of process reliability
Sensors
- Visionline F100S, scanning width 100 mm
- Visionline F200S, scanning width 200 mm
- Visionline F400S, scanning width 400 mm
Downloads
优点
- 高分辨率:即使小缺陷也可以检测到。
- 不依赖于操作员:用全面的 360° 视图自动检查内孔表面。
- 高质量:保持高质量要求。
- 可靠:质量持续得到检查并保持一致。
- 模块化:独立系统或生产线集成的检查机器。
- 易于使用:检查系统易于操作。Optisens 软件在评估过程中提供帮助。
应用
- 汽车工业、机械工程、医疗技术:功能部件表面的视觉检查。
请联系我们的专家,获得相关建议!
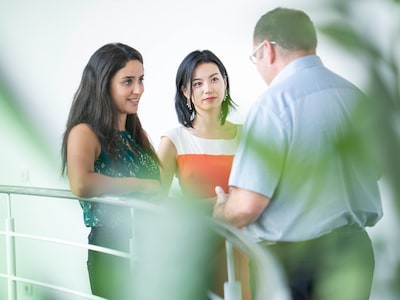
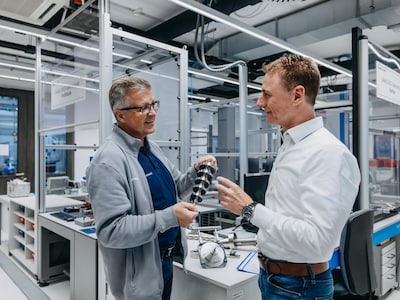
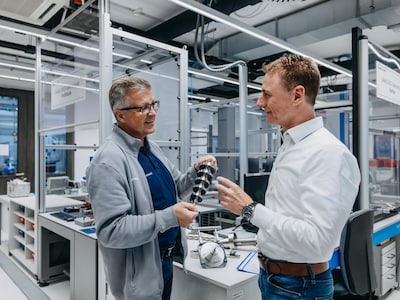
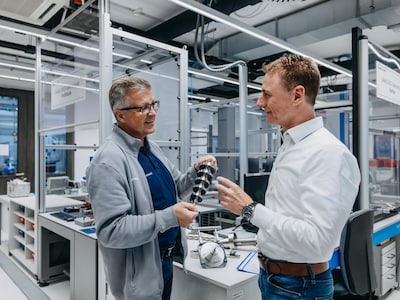
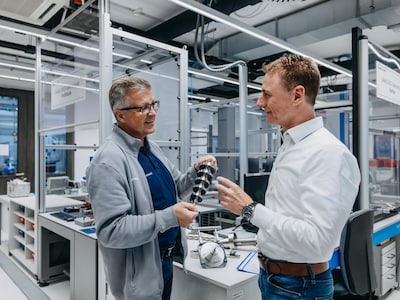
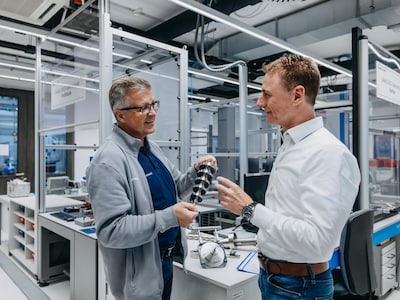
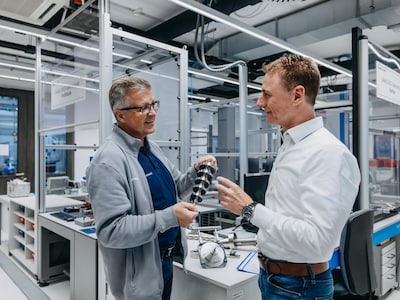